Removing Corrosion & Coatings
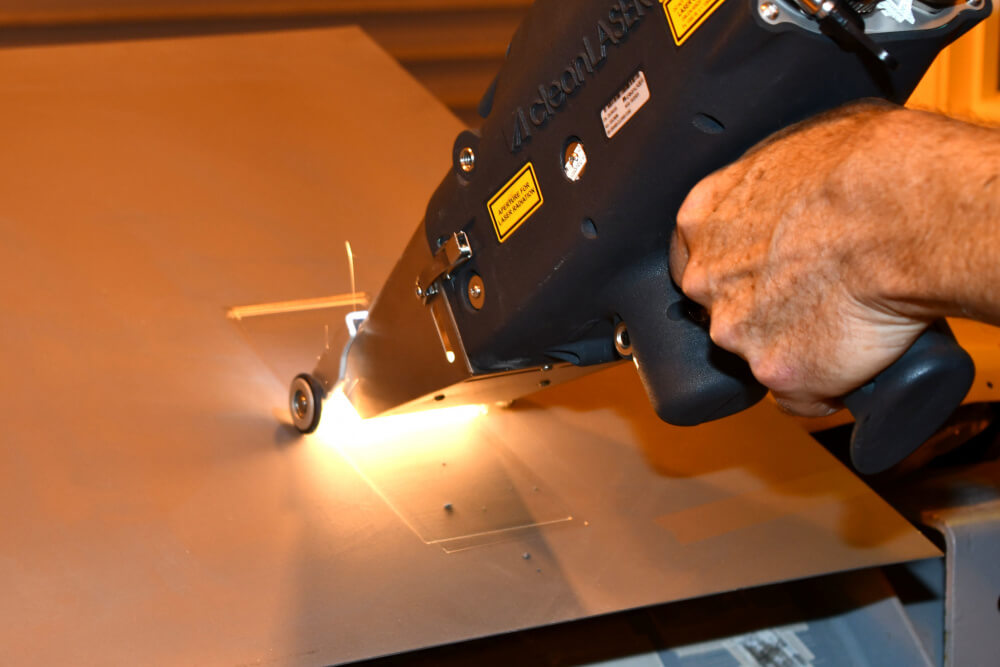
From warships to aircraft and everything in between, military vehicles are built to withstand the hardships of combat and extreme environmental elements. Part of this process includes coating equipment with a protective layer that helps to keep paint looking fresh and reduce the effects of corrosion. But, sometimes rust can still occur, and the corrosion and old protective coating needs to be removed and a new coat applied to sustain the lifespan of the equipment.
When this happens, the Fleet Readiness Center East (FRCE) is responsible for removing coatings and maintaining multiple military aviation assets for the US Navy and Marine Corps. Typically, this involves using plastic blasting and mechanical removal methods. But, the processes have proven to be slow, expensive, loud, and less safe than other alternatives. FRCE’s Advanced Technology and Innovation Team and Materials Engineering Division have been working for some time to bring laser ablation technology to the facility, and they finally got their chance in 2020.
DEMONSTRATING THE POWER OF A LASER SOLUTION
The Adapt Laser team held a demonstration at Marine Corps Air Station Cherry Point, NC. At the demonstration, we used a CL1000 laser solution to show how easily and quickly the application could be used to remove contaminants from aircraft components. Using our robust and proven laser cleaning solutions, the handheld optics were used to simultaneously emit laser light that is absorbed into the coatings/contaminants to free them from the surface and to capture all of the dangerous coatings at the point of cleaning.
Our laser solutions use state-of-the-art air filters to safely capture hazardous particles. These filters are easier to remove and dispose of, making the entire process easier and less expensive for the FRCE team. In addition to being safer to remove hazardous coatings, operators were only required to wear laser safety glasses. This means less bulky and constricting PPE when compared with plastic blasting.
RESULTS THAT SPEAK FOR THEMSELVES
The laser solution demonstration checked all of the boxes for the FRCE team. Previously, they dealt with a cleaning solution that was loud, expensive, dirty, and less safe for operators. But, our laser cleaning solution proved to be almost the exact opposite of their pain points. The solution is quieter, quicker, more effective, produces little to no waste, and is safer to operate.
While the initial price of our CL1000 handheld laser cleaning solution typically costs around $500,000, FRCE engineers say they expect the system would pay for itself in the long run. With reduced costs for purchase and disposal of hazardous materials, as well as the benefits of quicker turnaround time, improved worker safety, and decreased environmental hazards, the laser system tends to pay for itself relatively quickly.
Initially, the FRCE team would use our handheld laser systems in the packaging and preservation shop to use on engine cans and, possibly, on some ground support equipment. But, once the research is complete, they plan to move forward using our systems on components, unmanned aerial vehicles, and the final goal, to clean a full aircraft using a robotic laser ablation system. For more information about our demonstration at the Marine Corps Air Station, read the full story here.