USAF AGE Corrosion Control
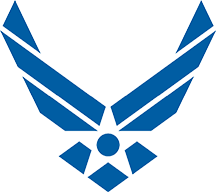
LASER ABLATION: AN ADOPTED PROCESS BY THE USAF
At Adapt Laser, we’re proud to provide laser solutions for the United States Air Force – specifically, for corrosion control on their aerospace ground equipment (AGE).
Traditionally, whenever aircraft equipment would experience rust or corrosion, professional cleaners would have to wear a moon suit and respirators and take the affected aircraft to a climate-controlled enclosed location to use sand blasters to eliminate rust. It was a slow and painful process that sometimes affected the item’s metal and leave behind hazardous waste.
Our laser cleaning systems ablate rust down to the metal without affecting its integrity, and the only safety equipment necessary are eye protective glasses. In addition, there’s no sand, paint, or hazardous waste to dispose. It’s clean, safe, effective and significantly faster than with any other method of removing corrosion.
HOW CLEANING LASERS ARE BEING USED BY USAF
The airmen at Travis Air Force Base trust our cleaning lasers on all their aerospace ground equipment (AGE) for paint removal and corrosion control. The CL300 mid-power laser and CL1000 high-power laser give them both the precision and power they need to clean support equipment — including hydraulic carts, AC units, power generators, and more.
Whereas traditional blasting and grinding techniques rely on abrasion to clean surfaces, our laser cleaning solutions send pulses of light onto the surface, effectively vaporizing the layers of rust or hazardous paint, without harming the substrate. Through carefully calibrated optics and fume extractors, our cleaning lasers provide an incredibly precise cleaning solution that produces minimal to no waste.
BENEFITS OF CLEANING LASERS FOR USAF CORROSION CONTROL
Before laser cleaning, the airmen relied on orbital sanders and sandblasting to remove paint and rust from their equipment. While effective, these traditional cleaning solutions have several drawbacks, such as:
- Creating lots of waste, resulting in a time-consuming cleanup
- A hazardous work environment, requiring extensive personal protective equipment (PPE) — a full Tyvek suit, face respirator, forced air respirator, and nitrile gloves
- Damages/removes the metal surface in addition to corrosion and paint
Laser cleaning, on the other hand, provides several advantages over conventional methods. With built-in fume extractors, laser cleaners not only produce less waste, they also clean it up. Results from the CL1000 laser showed a 90% reduction in waste when compared to sanding treatments. Laser cleaning also is able to remove the paint and rust layers without damaging the metal substrate, allowing for non-destructive investigation (NDI) and increasing the overall parts life cycle of the equipment.
For operators, laser cleaning is also much safer than sanding methods. Instead of extensive PPE, all that is required is specialized glasses, hearing protection, and gloves. This also allows for more efficient equipment maintenance since there is no substantial setup and teardown time required to operate the lasers.