Laser Ablation Proves Effective for DOT Bridge Project
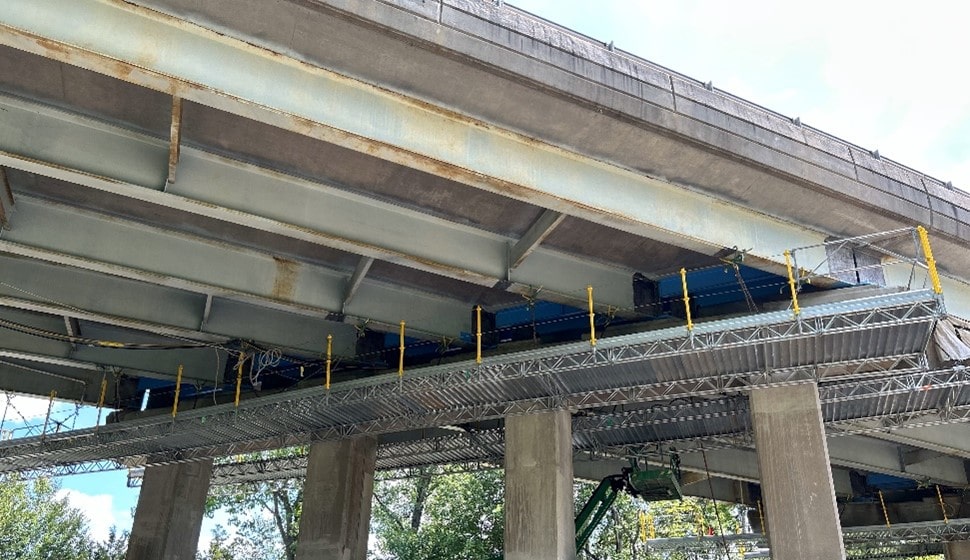
THE CHALLENGE
To validate advanced surface preparation technology using laser ablation coating removal (LACR) on-site as part of an innovative bridge preservation project for the Connecticut DOT. Coatings to be removed were considered to be hazardous as they may contain lead. The selected highway bridge was over a two-lane road and pedestrian walkway, both active during the entire project. LACR was specified as a pilot project to assess its feasibility and potential to save the State time and money, including environmental benefits compared to traditional abrasive blasting or power tools.
PROJECT DETAILS & OVERVIEW
Client: Connecticut DOT | Laser Ablation Contractor: Best-Tec | Location: Plantsville, CT
The specific location for the project was the on-ramp from Mulberry to I-84 that crosses Canal Street and the Farmington Canal Heritage Trail which includes a pedestrian walkway and biking path. This bridge project involved repairing the corrosion damaged ends of 36” steel H beams using cast in-place ultra-high strength concrete. Surface preparation required removing the existing paint and rust 26” from the beam ends using LACR at 36 locations prior to welding shear pins to the beam web. In addition, paint removal was necessary to comply with OSHA and environmental regulations due to the possible presence of paint containing lead, or other hazardous metals. Temporary decking suspended from the bridge beams provided access to the work areas. Laser ablation equipment was delivered to the site and operated from within an enclosed trailer which provided protection and security. The equipment trailer was placed where it did not interfere with traffic or use of the pedestrian walkway.
The LACR work for this project was estimated to take 15 days to complete.
LASER ABLATION PROCESS
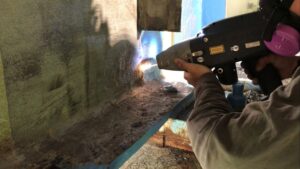
An Adapt Laser, 1000-watt, high power laser system was specified to treat the corrosion damaged beams. The laser power supply remains in the equipment trailer while the beam is delivered by a fiber optic cable to a hand-held laser end effector. The laser system used on this project was equipped with two 150-foot-long fiber optic cables and two laser end effectors. One end effector designed for treating easy access areas, the other designed to treat hard access areas.
Technicians sweep the scanned laser beam over the surface removing paint and rust to expose clean base metal. Using only focused light, the laser beam vaporizes organic coatings and rust without removing any base metal. Vaporized paint and rust residues are captured immediately at the laser end effector by suction from a laser fume extractor filter unit. The laser fume extractor has 3 stages of filtration. The first consists of particle filters with a self-cleaning mechanism to maintain optimal performance, the next filter stage contains activated carbon for gas followed by a third stage HEPA filter.
Advantages of Laser Ablation:
- Provides a clean and contaminant free surface with little or nothing to clean-up.
- Mitigates environmental risks associated with lead paint removal.
- Uses no consumable blast media or chemicals.
- Creates no mixed secondary waste to collect and dispose.
- Does not remove or damage the base metal.
- Does not require dust containment.
- Can be operated near and around other activities using laser safety curtains.
- Operates at a much lower noise level compared to abrasive blasting or needle guns.
- Has a small equipment footprint on-site to eliminate or minimize the need for road closures.
ENVIRONMENTAL, HEALTH, & SAFETY
Environmental
Environmental concerns are often one of the most complex aspects during maintenance operations on older bridge structures as encountering lead-based paint is very likely. Traditionally, State Departments of Transportation (DOTs) have relied on sandblasting and re-painting to combat corrosion.
However, this conventional process has drawbacks like:
- Frequent lane closures to isolate and capture media and other hazardous coatings produced during the paint stripping process
- Safe collection and disposal methods require special packaging that have significant costs
LACR addresses the environmental concerns associated with bridge preservation projects by:
- Cutting out grit blasting and the large waste stream of media it creates
- Eliminating the need for an elaborate containment system by capturing emissions at the source
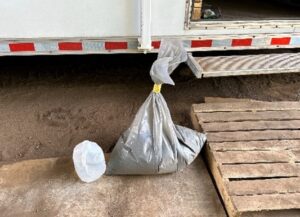
For this project, LACR provided a major reduction in process waste compared to similar sized projects employing sandblasting. Discussions with personnel from another project revealed sandblasting would have generated approximately six 55-gallon drums of spent blast media mixed with hazardous paint residue. Each drum would weigh approximately 1,500 to 2,000 lbs, necessitating 9,000 to 12,000 lbs. of waste disposal.
The use of laser ablation at this project significantly minimized waste generation. At the completion of the work, the waste generated by LACR was approximately 40 lbs. of dry powder with a waste reduction of over 99%.
Health & Safety
Compared with traditional surface prep methods, LACR with fume extraction on bridge projects offers significant worker health and safety benefits. These include reduced personal protective equipment (PPE) requirements, mitigating the exposure risks to harmful airborne substances, and noise reduction.
LACR PPE Requirements Can Include:
- Eye Protection—for most applications not involving hazardous coatings, laser operators typically only need to wear laser safety glasses
- Laser Safety Area—Laser safety curtains are used to prevent possible beam exposure from other nearby personnel when not in a fully enclosed area
- Respiratory Protection—When removing hazardous coatings, such as lead paint, a half-face respirator with HEPA and vapor filters is recommended; normal coatings during LACR don’t require a respirator
- Hearing Protection—Most times noise levels are consistently below 85 dB, thus eliminating the need for hearing protection
- Public Safety—For the project, visible emissions resulting from the laser operation were absent, allowing pedestrians to safely pass by the work area
CONCLUSION
The project was safely and successfully completed one day ahead of the initial planned duration of 15 working days and validates the benefits and practical applications of LACR in a real-world scenario for bridge maintenance and preservation projects. It verified the feasibility of using the process in remote working environments, with significant waste stream reduction, mitigation of emissions, small equipment laydown requirements, minimized lane closures and improved accessibility to tight spaces.
Transportation agencies now have a useful example of how LACR offers a new solution for maintaining our aging infrastructure with advanced technology that saves time and money while helping to protect the planet.