Laser Lead Abatement
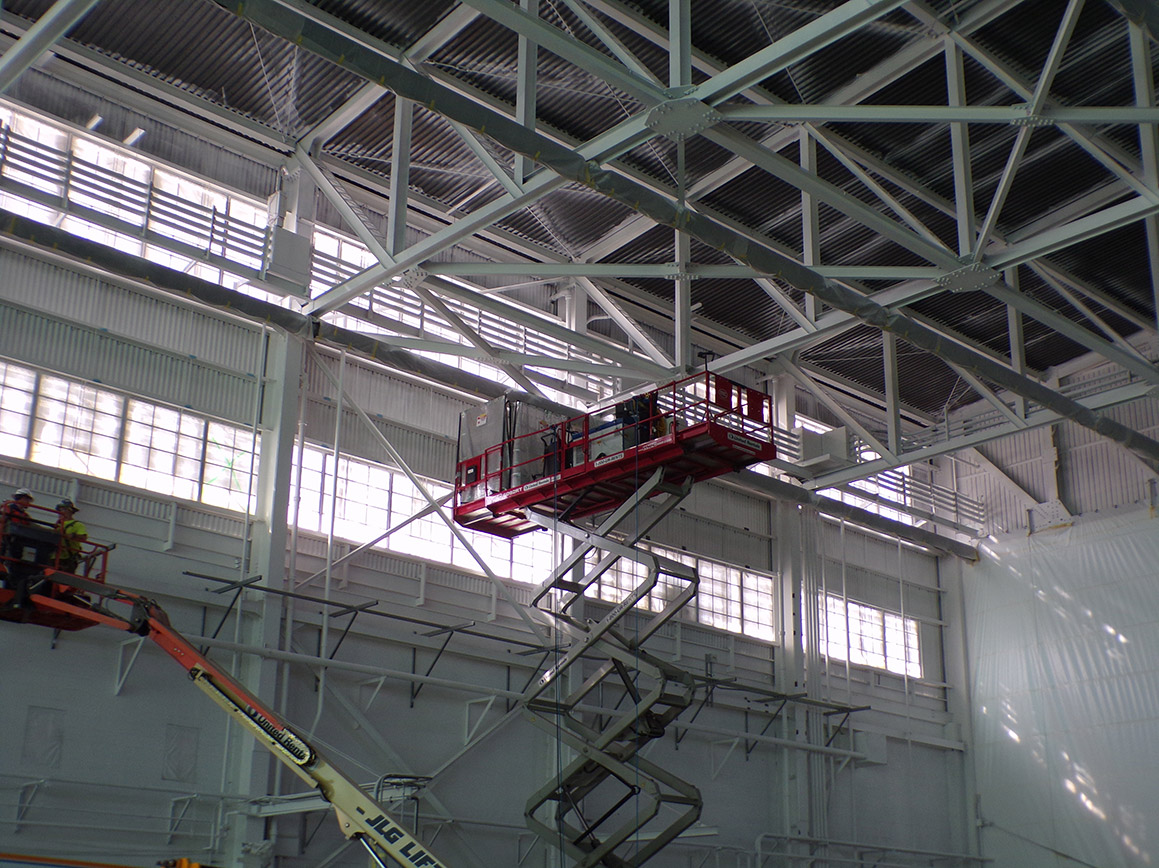
THE CHALLENGE
PROJECT DETAILS
The hangar dimensions posed specific challenges to using traditional methods inside an occupied building, such as paint stripping, needle gun scaling, and abrasives.
Hangar dimensions:
- Length: 600 ft
- Width: 165 ft
- Ceiling Height: 45 ft
- Overall Height: 78 ft
METHODS USED PRIOR TO LASER CLEANING
Regular operations within the hangar require the cleaning and disposal of multiple types of hazardous and regulated materials. Abrasive blasting techniques would require complex and cumbersome containment setups to capture both the lead paint chips and the blast medium. Likewise, traditional hand grinders create a large amount of lead dust, which is impractical and unsafe for an occupied building without similar containment setups.
The most common option employed by the hangar personnel before laser cleaning was chemical paint stripping. This method avoided the need for a containment setup, but required a substantial downtime for the chemicals to remove the paint — about 12 hours. Due to the thickness of the paint, this meant an average of 3 applications of chemicals for an effective cleaning. Employees were also required to wear extensive PPE when working with the chemicals. Another downside to chemical stripping is the hazardous waste created during the process, which then has to be disposed of safely. Eventually, the time burden and risk to operators made this a poor option for hangar operations in the long run.
TRANSITIONING TO LASER CLEANING
DECIDING TO MAKE THE CHANGE
After researching alternative cleaning options, the client decided to test using a high power laser for their project. To test the viability of laser cleaning for the lead removal, they brought some sample pieces of steel with comparable coatings to Adapt Laser for an in-person lab test and demonstration. In the lab testing, the lasers were able to effectively remove the layers of hazardous coating with an incredibly high level of success. The cleaning lasers were also able to minimize employee exposure to hazardous particles in the air through their built-in fume extraction filters.
“The results were nothing less than stunning. The paint was literally vaporizing in front of my eyes”
– Client, upon seeing the lasers in action
GETTING APPROVAL FOR USE
Because portable, high-powered lasers are not commonplace in a jobsite, the client had to gather extensive data and technical specifications to show the feasibility of laser cleaning for the project. Though comparable use cases for laser cleaning were not available in large quantities, the positive results shown in the data were ultimately enough to gain approval for the hangar.
They outlined a laser work plan and created a specialized laser containment, which consisted of laser curtains and supports attached to the scissor lift, boom lift, and existing structural elements. They also performed continuous air testing daily to make sure the workers’ breathing zone was safe. Findings showed that proper use of laser and fume extraction produced lower lead readings than employees hand-scraping loose paint chips.
USING THE LASERS IN SITU
Whereas the lab testing is done in a stable, controlled environment and operated by experts, the actual laser cleaning would be done in a regular work environment by operators without any field experience with lasers. The indoor height of the hangar (from 48ft to 78ft) meant lifting the laser cleaner, fume extractor, and all of its accessories to the contaminated areas.
Once the machine was in place, the laser operator would retrieve the laser optic from the scissor lift via the boom lift and begin the cleaning process. The boom lift allowed the operator the ability to move roughly 30ft in all directions around the laser platform.