Lead-Bearing Paint Abatement Using Laser Ablation: At An Operating Nuclear Power Plant
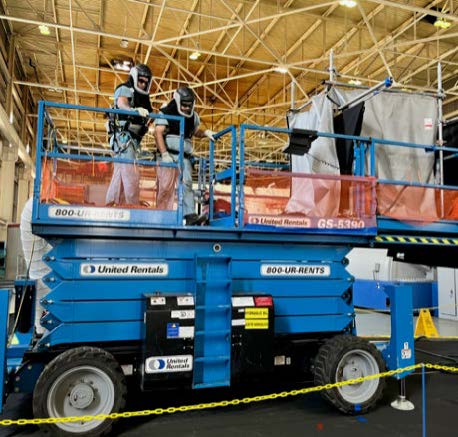
THE CHALLENGE
PROJECT DETAILS
Client: Dominion Energy | Contractor: Day & Zimmerman | Location: Dominion Surry Nuclear Plant – The Turbine Building
The Turbine Building houses two overhead cranes spanning 133 feet with each crane having two girders with rails that the trolley rests and travels on. The girders are ~48 feet above the turbine deck. During the lead abatement process, the area was broken into 6in strips on both sides of the rail that runs centerline on the 36in wide girder.
Total Areas Requiring Abatement:
- ~399 sq. ft. on the girder surface
- ~21 sq. ft. under the trolleys
- the 92 clips holding down each of the four rails along the weld joint
The project was scheduled to start in July of 2023 but was moved into late August due to concerns over high temperatures. This delay compressed the time allowed to complete the work into six weeks.
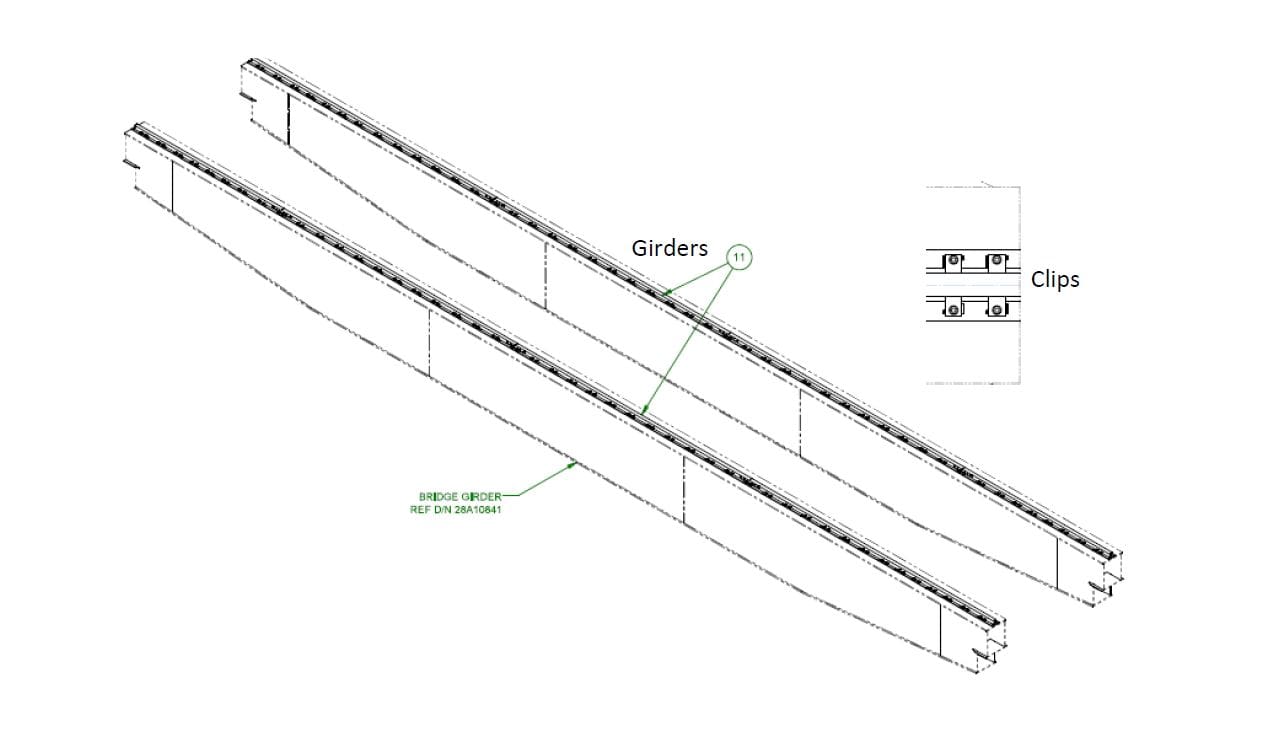
PROJECT OVERVIEW – USING LASER ABLATION TECHNOLOGY
The work was done by an on-site team consisting of a Laser Safety Officer (LSO), a working supervisor, and 3-5 laser operators. This team was assembled after the purchase of a CL1000, high power laser system from Adapt Laser back in 2021. The laser team is self sufficient in that they can operate and maintain the laser as well as qualify new operators.
Location and Access Constraints
- The work location being high in the overhead around operating turbine generators meant that no foreign material could be generated from mechanical removal of the paint.
- High ambient temperatures combined with the heat generated by the operating steam plants created temperatures that would require mitigating actions
- Being away from the home position limited access to either a temporary scaffold staircase or from a scissor lift
Equipment Challenges
- Due to 40 years of use, the cranes had an accumulation of dirt and dust on the top surfaces
- In the area where the trolley rests in the home position, years of grease coated the girder surface
- The paint thickness varied across the girders from 10 to 20 mils. The time to remove the paint is directly proportional to the thickness of the paint.
METHODOLOGY & INNOVATIVE SOLUTIONS
To overcome the different constraints and challenges the project’s location and equipment caused, a creative approach was taken.
- Access to the girders – the team designed and constructed a tent using laser safety curtains inside the lift that extended over the girder
- For cleaning the girder surface – a “clean-as-you-go” strategy was implemented from the scissor lift for the greasy areas
- To assist with control and positioning of the laser – a zero gravity arm was incorporated into the design which also helped increase operating times by bearing the weight of the laser
- Overheating of the equipment and personnel – to help cool the small chiller that keeps the laser cool, a larger chiller was placed at the turbine deck, with a trunk line running up. This solved the problem of the small chiller overheating and allowed a cooling station to be added for workers
- Handling variations in paint thickness – a commercial paint remover readily removed the paint helping to return productivity despite the 10-20 mil variation in the thickness of the paint
Laser ablation technology solved the big challenge associated with dust and debris that are caused from mechanical processes like needle guns. Using focused laser light, the laser beam vaporizes coatings like paint, oils, and greases without removing any of the base metal. Vaporized contaminants are then captured immediately at the laser end effector by suction from a laser fume extractor filter unit. The laser fume extractor has 3 stages of filtration. The first consists of particle filters with a self-cleaning mechanism to maintain optimal performance, the next filter stage contains activated carbon for gas followed by a third stage HEPA filter. This then empties into a dust collection drawer that can be removed and disposed of in the proper way.
Conclusion
Initially, the project planned to use mechanical methods—needle guns—to remove the lead-based paint and prepare surfaces for welding. However, this approach, constrained by ambient temperature limits on workers’ stay times, would have required a crew of 24-36 multi-skilled workers and increased the risk of heat-related injuries. By opting for laser ablation, the crew size was reduced to five. This innovation, coupled with a cooling station to mitigate heat stress, nearly doubled productivity. In-process lead sampling confirmed the laser’s effectiveness in reducing lead levels in the immediate work area.
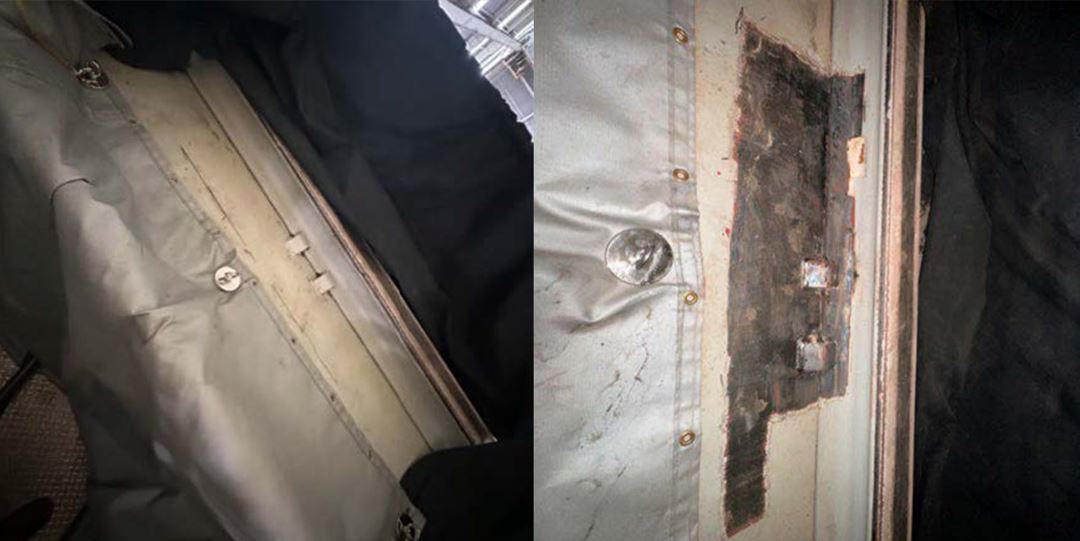
Lead Sample Data
Paint Test Results
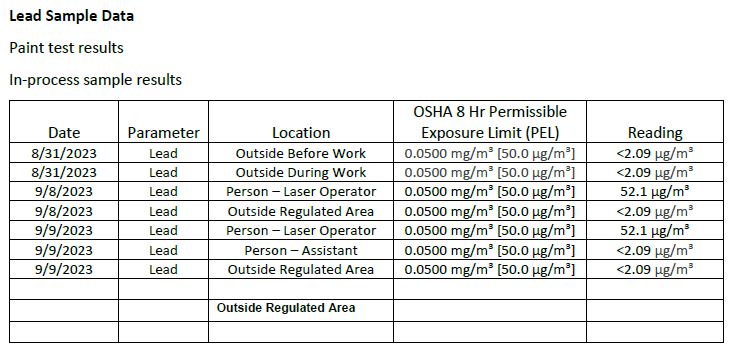
For more information on this project and other work we’ve done with nuclear applications please contact us for more details.