One of the biggest advantages laser cleaning has over its more traditional competitor—media blasting—is its lack of cleanup and coinciding environmental friendliness. Our ablation process involves suction and filtration as the method of capture and disposal for contaminants, and we take special consideration for hazardous gases and fumes. But how can suction options differ and how can you know when to use which?
HOW TO PROVIDE SUPERIOR SUCTION
One way that we have addressed problems surrounding suction is by designing interchangeable nozzles for our OSH20, OSH50, OSH80, and effiSCAN optics. Although there is no strict rule as to what nozzle to use for a certain application, we have seen the short used for more general use, the long for hazardous gases, and the roller to help with larger pieces that may ignite operator fatigue. The standard three nozzles available for the OSH50 are the short, long, and roller options. The OSH80 works with the short and roller nozzles in addition to the nuclear decontamination nozzle that is still currently going through development and redesign phases. Our newest and most portable optic—the effiSCAN—works with the short and roller nozzles.
WHY IS SUCTION IMPORTANT?
When removing contaminants from your substrate, you’ll need a way to contain all of the particles that are being ablated. By using the nozzle that best aligns with your application needs, you can can help alleviate problems later on such as operator safety concerns, environmental risks, dirtying the protection window, and proper contaminant extraction. Even if the contaminants being removed aren’t harmful to inhale, they will still need to be properly captured, removed, and then disposed of.
Throughout the laser cleaning process you will encounter different fumes, particles, dust, and potentially other hazardous chemicals that will require filtration. We exclusively partner with TEKA for all of our fume extraction needs as they are state-of-the-art systems that are programmed to integrate directly into our laser cleaning systems.
NOZZLE DIFFERENCES
Short (Standard)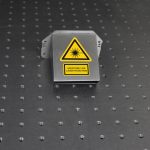
- The short nozzle is the standard nozzle that comes with the OSH50 and OSH80 optics. This nozzle is good to use for molds, on smaller areas of material, or when you may need better visualization as you work. For example, the short and roller nozzles work together well on curved and more complex parts, as the short nozzle provides accessibility and a good visual while the roller nozzle provides speed efficiency while remaining ergonomically friendly to the operator.
Long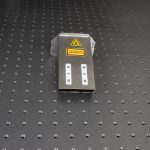
- The long nozzle is designed to catch the hazardous gases, dusts, fumes, and chemicals that may become airborne during the laser cleaning process. It helps remove contaminants at the source of ablation before there’s a chance for it to create a plume cloud.
Roller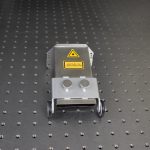
- The roller nozzle was designed to help maintain focus throughout the cleaning process. The nozzle helps hold the weight of the optic so it’s best to use on large, flat surfaces that just require a steady motion.
NOZZLES IN ACTION
The picture above was taken after ablating a line using all three nozzles on a steel plate with thick black paint as the contaminant. This particular testing used our OSH50 optic attached to our CL300 cleaning system.
- The line on the left was ablated by the short nozzle and you can see where the operator was able to remain in-focus and keep a steady, consistent clean.
- In comparison, the line in the middle was ablated by the long nozzle—meaning it extracted the affluent directly at the source, but affected visibility as it did—causing it to be a less consistent, linear clean.
- Notice on the right, the roller nozzle cleaned the surface with more consistent movements and path linearity. The roller nozzle is essentially the long nozzle with two wheels strapped to it, providing an ergonomically friendly way to clean large, flat areas.
WHATEVER YOUR NEEDS, ADAPT LASER HAS THE SOLUTION FOR IT
Adapt Laser specializes in providing the highest-quality laser cleaning systems available. Our systems come in both handheld and automated options making them versatile for different applications and surface preparation. We offer operations and safety training to ensure both you and your employees get the most out of their laser cleaning system. Over the past 15 years we have helped equipped numerous companies across varying industries with our state-of-the-art laser cleaning solutions.
If you’re looking for a faster cleaning process, contact us today or call (816) 466-5855 to find the right laser cleaning system for you.
Like us on Facebook, connect with us on LinkedIn, and subscribe to us on YouTube